ГОСТ Р
ИСО 1817-2009
Группа
Л69
НАЦИОНАЛЬНЫЙ СТАНДАРТ
РОССИЙСКОЙ ФЕДЕРАЦИИ
РЕЗИНА
Определение
стойкости к воздействию жидкостей
Rubber.
Determination of resistance to liquids effect
ОКС
83.060
ОКСТУ 2509
Дата
введения 2011-01-01
Предисловие
Цели
и принципы стандартизации в Российской
Федерации установлены Федеральным
законом от 27 декабря 2002 г. N 184-ФЗ "О
техническом регулировании", а правила
применения национальных стандартов
Российской Федерации - ГОСТ Р 1.0-2004
"Стандартизация в Российской Федерации.
Основные положения"
Сведения
о стандарте
1
ПОДГОТОВЛЕН Техническим комитетом по
стандартизации ТК 080 "Резиновые
технические изделия" (Обществом с
ограниченной ответственностью
"Научно-исследовательский институт
эластомерных материалов и изделий"
- ООО "НИИЭМИ") на основе собственного
аутентичного перевода на русский язык
стандарта, указанного в пункте 4
2
ВНЕСЕН Управлением технического
регулирования и стандартизации
Федерального агентства по техническому
регулированию и метрологии
3
УТВЕРЖДЕН И ВВЕДЕН В ДЕЙСТВИЕ Приказом
Федерального агентства по техническому
регулированию и метрологии от 15 декабря
2009 г. N 1136-ст
4
Настоящий стандарт идентичен международному
стандарту ИСО 1817:2005* "Резина. Определение
стойкости к воздействию жидкостей"
(ISO 1817:2005 "Rubber, vulcanized - Determination of the effect
of liquids").
________________
*
Доступ к международным и зарубежным
документам, упомянутым здесь и далее
по тексту, можно получить, перейдя по
ссылке. - Примечание изготовителя базы
данных.
При
применении настоящего стандарта
рекомендуется использовать вместо
ссылочных международных стандартов
соответствующие им национальные
стандарты Российской Федерации и
межгосударственные стандарты, сведения
о которых приведены в дополнительном
приложении ДА
5
ВВЕДЕН ВПЕРВЫЕ
Информация
об изменениях к настоящему стандарту
публикуется в ежегодно издаваемом
информационном указателе "Национальные
стандарты", а текст изменений и
поправок - в ежемесячно издаваемых
информационных указателях "Национальные
стандарты". В случае пересмотра
(замены) или отмены настоящего стандарта
соответствующее уведомление будет
опубликовано в ежемесячно издаваемом
информационном указателе "Национальные
стандарты". Соответствующая информация,
уведомление и тексты размещаются также
в информационной системе общего
пользования - на официальном сайте
Федерального агентства по техническому
регулированию и метрологии в сети
Интернет
Введение
В
результате воздействия жидкости на
резину может произойти:
а)
поглощение жидкости резиной;
б)
экстракция растворимых компонентов из
резины;
в)
химическая реакция с резиной.
Обычно
поглощение жидкости резиной превышает
экстракцию растворимых компонентов из
резины, поэтому суммарный результат
выражается в увеличении объема, которое
называется "набухание". Поглощение
жидкости может привести к значительным
изменениям физических и химических
свойств и, следовательно, к изменению
таких показателей, как предел прочности
при растяжении, деформация и твердость
резины, поэтому важно провести измерение
этих показателей после "набухания"
резины. Экстракция растворимых
компонентов, особенно пластификаторов
и противостарителей, может таким же
образом изменить физические свойства
резины и химическую стойкость после ее
высушивания (допуская, что данная
жидкость летучая). Поэтому необходимо
проверить эти свойства после погружения
резины в жидкость или после ее высушивания.
Настоящий стандарт устанавливает
методы, необходимые для определения
изменений следующих свойств:
-
массы, объема и размеров;
-
массы веществ, экстрагированных средой;
-
твердости и деформационно-прочностных
свойств при растяжении после погружения
в жидкость и после погружения в жидкость
с последующим высушиванием.
Хотя
в некоторой степени подобные испытания
могут моделировать условия эксплуатации,
прямой корреляции с поведением во время
эксплуатации не подразумевается. Таким
образом, резина, в меньшей степени
подверженная изменению объема, не всегда
является наилучшей в эксплуатации.
Следует учитывать толщину резины, так
как скорость проникновения жидкости
зависит от времени и объема. Изделия из
резины очень большой толщины могут не
подвергаться воздействию жидкости в
течение всего предполагаемого срока
эксплуатации, особенно это касается
вязких жидкостей. Более того, известно,
что присутствие атмосферного кислорода
может оказать влияние на процесс
воздействия жидкости на резину, особенно
при высоких температурах. Испытания по
настоящему стандарту могут предоставить
важную информацию о возможности
применения резины при контакте с
определенной жидкостью и, в частности,
обеспечить необходимый контроль при
разработке резины, стойкой к маслам,
топливу или другим рабочим жидкостям.
Воздействие
жидкости может зависеть от природы и
вида созданного напряжения в резине. В
настоящем стандарте испытания проводят
на образцах резины в ненапряженном
состоянии.
В
настоящем стандарте не предусмотрено
рассмотрение всех вопросов обеспечения
безопасности, связанных с его
использованием. За установление норм
безопасности и охраны здоровья
ответственность несет испытатель.
1
Область применения
Настоящий
стандарт устанавливает методы оценки
стойкости резины к воздействию жидкостей
путем определения свойств резины до и
после погружения в жидкость для испытаний.
Для испытаний применяют рабочие жидкости,
такие как производные нефти, органические
растворители и химические реактивы, а
также стандартные жидкости для испытаний.
2
Нормативные ссылки
В
настоящем стандарте использованы
нормативные ссылки на следующие
международные стандарты :
_______________
*
Для датированных ссылок используют
только указанное издание стандарта. В
случае недатированных ссылок - последнее
издание стандарта, включая все изменения
и поправки.
**
Таблицу соответствия национальных
стандартов международным см. по ссылке.
- Примечание изготовителя базы данных.
ИСО
37 Каучук вулканизованный или
термопластичный. Определение механических
свойств при растяжении (ISO 37, Rubber,
vulcanized or thermoplastic - Determination of tensile stress-strain
properties)
ИСО
48 Каучук вулканизованный или
термопластичный. Определение твердости
(от 10 до 100 IRHD) [ISO 48, Rubber, vulcanized or thermoplastic
- Determination of hardness (hardness between 10 IRHD and 100 IRHD)]
ИСО
175 Пластмассы. Методы испытаний для
определения стойкости к погружению в
жидкие химикаты (ISO 175, Plastics - Methods of test
for the determination of the effects of immersion in liquid
chemicals)
ИСО
2592 Определение вспышки и температуры
воспламенения. Метод с применением
прибора Кливленда с открытым тиглем
(ISO 2592, Determination of flash and fire points - Cleveland open
cup method)
ИСО
2977 Нефтепродукты и углеводородные
растворители. Определение анилиновой
точки и анилиновой точки смеси (ISO 2977,
Petroleum products and hydrocarbon solvents - Determination of
aniline point and mixed aniline point)
ИСО
3016 Нефтепродукты. Определение температуры
текучести (ISO 3016, Petroleum products - Determination of
pour point)
ИСО
3104 Нефтепродукты. Прозрачные и непрозрачные
жидкости. Определение кинематической
вязкости и расчет динамической вязкости
(ISO 3104, Petroleum products - Transparent and opaque liquids -
Determination of kinematic viscosity and calculation of dynamic
viscosity)
ИСО
3675 Нефть сырая и жидкие нефтепродукты.
Лабораторное определение плотности.
Метод с применением ареометра (ISO 3675,
Crude petroleum and liquid petroleum products - Laboratory
determination of density - Hydrometer method)
ИСО
5661 Нефтепродукты. Углеводородные
жидкости. Определение коэффициента
преломления (ISO 5661, Petroleum products - Hydrocarbon
liquids - Determination of refractive index)
ИСО
23529:2004 Резина. Основные процедуры
приготовления и кондиционирования
испытательных образцов для физических
испытаний (ISO 23529:2004, Rubber - General procedures for
preparing and conditioning test pieces for physical test methods)
3
Аппаратура
3.1
Устройство для полного погружения
образца, которое сконструировано с
учетом летучих свойств жидкости для
испытания и необходимости поддержания
температуры для предотвращения и
снижения до минимума испарения жидкости
и проникновения воздуха.
Для
испытаний при температурах значительно
ниже точки кипения жидкости используют
закрытые пробкой склянки или пробирки.
Для испытаний при температурах, близких
к точке кипения жидкости, к склянке или
пробирке присоединяют обратный
холодильник или используют другие
средства для сведения к минимуму
испарение жидкости.
Склянка
или пробирка должны иметь такие размеры,
чтобы образцы для испытаний оставались
полностью погруженными и подвергались
воздействию жидкости свободно, без
ограничений. Объем жидкости должен
превышать суммарный объем образцов для
испытаний не менее чем в 15 раз, а объем
воздуха над жидкостью должен быть
минимальным.
Образцы
для испытаний должны быть закреплены
в держателях, предпочтительно подвешенных
на стержне или проволоке, и отделены от
соседних образцов стеклянными кольцами
или другими инертными распорками.
Материалы
для оборудования должны быть инертными
по отношению к жидкости для испытания
и резине, например нельзя использовать
материалы, содержащие медь.
3.2
Устройство для испытания только одной
поверхности
Устройство,
которое обеспечивает контакт с жидкостью
только одной из поверхностей образца
для испытания, приведено на рисунке 1.
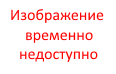
1 -
опорная плита; 2 - цилиндрическая камера;
3 - образец для испытания; 4 - крыльчатая
чайка; 5 - болт; 6 - пробка
Рисунок 1 -
Устройство для испытания только одной
поверхности
Устройство
состоит из опорной плиты 1 и открытой с
торцов цилиндрической камеры 2, которая
плотно прижата к образцу для испытания
3 с использованием крыльчатых гаек 4,
установленных на болтах 5. Для осмотра
поверхности, не соприкасающейся с
жидкостью, на опорной плите имеется
отверстие диаметром около 30 мм. Во время
испытания отверстие верхней части
камеры должно быть закрыто плотно
пригнанной пробкой 6.
3.3
Весы с погрешностью измерения не более
±0,001 г.
3.4
Прибор для измерения толщины образца
для испытания, состоящий из микрометра
с круговой шкалой требуемой точности,
прочно укрепленной на жесткой стойке
над плоской опорной плитой.
Цена
деления шкалы микрометра должна быть
0,01 мм. Плунжер должен быть снабжен
плоским круглым контактом с площадью
поверхности около 100 мм .
Контакт должен располагаться
перпендикулярно к плунжеру и параллельно
опорной плите. Прибор с круговой шкалой
должен оказывать давление на резину,
равное примерно 2 кПа.
3.5
Прибор для измерения длины и ширины
образца для испытания, имеющий шкалу с
ценой деления 0,01 мм и работающий без
контакта с образцом, например используя
оптическую систему.
3.6
Прибор для измерения площади поверхности
образца, способный измерить длину
диагоналей образцов для испытаний.
Прибор
должен иметь шкалу с ценой деления 0,01
мм и работать предпочтительно без
соприкосновения с испытуемым образцом,
например используя оптическую систему.
4
Жидкости для испытания
Выбор
жидкости для испытания должен зависеть
от цели испытания.
Если
требуется получить информацию о поведении
резины при эксплуатации в контакте с
определенной жидкостью, то следует
выбирать для испытания, по возможности,
именно эту жидкость. Товарные жидкости
не всегда имеют постоянный состав,
поэтому при проведении испытаний
рекомендуется использовать для контроля
стандартные жидкости с известными
характеристиками. Минеральные масла и
топлива, поставляемые по одним нормативным
документам, значительно различаются
по химическому составу. Анилиновая
точка минерального масла является
показателем содержания ароматических
веществ и помогает характеризовать
воздействие данного масла на резину.
При использовании в качестве жидкости
для испытания минерального масла
протокол испытания должен включать:
плотность, показатель преломления,
вязкость и анилиновую точку или содержание
ароматических соединений в данном
масле. В качестве стандартных масел,
приведенных в приложении А, применяют
рафинированные минеральные масла.
Рабочие
масла, имеющие характеристики текучести,
аналогичные стандартным маслам
(приложение А), не обязательно будут
воздействовать на резину аналогично
стандартным жидкостям. Некоторые виды
топлива, в частности бензин, различаются
по составу, при этом даже незначительные
различия в составе могут привести к
разному воздействию топлива на резину.
В связи с этим в протокол испытания
необходимо включать подробную
характеристику испытуемого топлива.
Для
классификации или контроля качества
резин должны использоваться стандартные
жидкости, состоящие из точно установленных
химических соединений или смесей
соединений.
При
проведении испытаний для определения
воздействия химических растворов на
резину массовая доля вещества в растворе
должна соответствовать предполагаемому
использованию.
Состав
жидкости для испытания не должен
изменяться во время погружения образца.
Необходимо учитывать изменение состава
жидкости для испытания и взаимодействие
жидкости с образцами для испытания. При
наличии в жидкости химически активных
добавок или при значительном изменении
ее состава в результате экстракции,
поглощения или химической реакции с
резиной необходимо увеличить объем
жидкости для испытания или заменять
жидкость на новую через определенные
интервалы времени.
5
Образцы для испытания
5.1
Приготовление образцов
Образцы
готовят в соответствии с ИСО 23529.
5.2
Размеры
Результаты,
полученные при испытании образцов
различной первоначальной толщины, могут
быть несопоставимыми. Поэтому образцы
для испытаний должны иметь толщину
(2,0±0,2) мм.
Можно
использовать образцы для испытаний,
вырезанные из изделий. Для изделий,
имеющих толщину менее 1,8 мм, используют
имеющуюся толщину. Если толщина образца
свыше 2,2 мм, то толщину уменьшают до
(2,0±0,2) мм. Допускается использовать
образцы толщиной 1,8 мм.
Образцы
для определения изменения объема и
массы должны иметь объем от 1 до 3 см .
Образцы
для определения изменения твердости
должны иметь длину, ширину и высоту не
менее 8 мм.
Образцы
для определения изменения размеров
должны иметь форму четырехугольника
со сторонами от 25 до 50 мм или кольца
внутренним диаметром 44,6 мм (внутренний
диаметр образца для испытания типа В
по ИСО 37). Такой тип образца для испытания
можно также использовать для определения
изменения массы и объема.
Образцы
для определения изменения площади
поверхности должны быть ромбовидными
со сторонами, аккуратно обрезанными
под углом 90° к верхней и нижней
поверхностям. Это может быть достигнуто
двумя последовательными срезами под
углом 90° друг к другу ножом с двумя
параллельными лезвиями, расположенными
подходящим образом. Номинальная длина
сторон должна быть 8 мм.
Примечание
- Для определения изменения площади
поверхности допускается использовать
более мелкие или тонкие образцы для
испытания, если они вырезаны из изделия
или если требуется быстрое достижение
равновесного состояния набухания.
Однако результаты могут оказаться
несопоставимыми с результатами,
полученными при использовании образцов
заданной толщины. Уменьшение размера
образцов для испытания снижает
сопоставимость результатов.
Образцы
для определения предела прочности при
растяжении должны соответствовать ИСО
37 (тип 2) и по возможности иметь гантелевидную
форму. Такой тип образца для испытания
можно также использовать при определении
изменений массы, объема или твердости.
При
испытаниях, в ходе которых в контакте
с жидкостью находится только одна из
поверхностей образца для испытания,
образец должен иметь форму круга
диаметром около 60 мм.
5.3
Интервал времени между вулканизацией
и испытанием
При
проведении испытаний минимальный
интервал времени между вулканизацией
и испытанием должен быть не менее 16 ч.
Для
испытаний, проводимых не на готовых
изделиях, интервал времени между
вулканизацией и испытанием должен быть
не более 4 недель, такое же время требуется
для оценки сопоставимости результатов.
Для
испытаний готовых изделий промежуток
времени между вулканизацией и испытанием
должен быть не более 3 мес. В других
случаях испытания должны проводиться
в течение 2 мес со дня получения резины
потребителем.
5.4
Кондиционирование
Образцы
резины должны быть выдержаны не менее
3 ч при температуре (23±2) °С или (27±2) °С.
Такую же температуру поддерживают при
любом испытании или серии испытаний,
чтобы результаты испытаний были
сопоставимыми.
6
Погружение в жидкость для испытания
6.1
Температура
Образцы
резины погружают в жидкость при одном
или нескольких значениях температуры,
указанных в ИСО 23529 (8.2.2).
Тщательно
подбирают температурный режим, так как
повышенные температуры могут значительно
увеличивать окисление резины, летучесть
или разложение жидкости для погружения
и воздействие любых химически активных
добавок, содержащихся в жидкости
(например, в рабочих жидкостях).
При
испытаниях, моделирующих условия
эксплуатации, с применением реальной
рабочей жидкости, с которой данная
резина будет использоваться, условия
испытаний должны быть приближены к
реальным условиям эксплуатации, включая
применение стандартной температуры,
которая должна быть равна или выше
рабочей температуры.
6.2
Время погружения
Так
как скорость проникновения жидкости в
резину зависит от температуры, типа
резины и типа жидкости, исключается
применение только одного периода
погружения. Для получения точных
результатов рекомендуется проводить
повторные измерения и записи после
каждого из последовательных периодов
погружения, чтобы зафиксировать изменение
свойств с течением времени. Полное время
погружения должно значительно превышать
точку максимального поглощения.
Для
контроля может быть достаточно одного
периода погружения, причем желательно
при этом достичь максимального поглощения.
Для этого необходимо проводить погружение
в течение одного из следующих периодов:
24
ч, 72
ч, (168±2) ч, кратный (168±2) ч.
Примечания
1
Так как количество первоначально
поглощенной жидкости пропорционально
квадратному корню времени погружения
в жидкость, а не самому времени, допускается
оценивать время, необходимое для
достижения максимального поглощения,
используя график зависимости количества
поглощенной жидкости от квадратного
корня времени погружения.
2
Изменение поглощения (в процентах) на
ранних стадиях погружения обратно
пропорционально толщине образца для
испытаний. Поэтому рекомендуется
применять образцы с меньшими предельными
отклонениями толщины для получения
сопоставимых результатов в случае, если
не достигнуто максимальное поглощение.
7
Методика проведения испытания
7.1
Подготовка к испытанию
Для
каждой серии измерений используют три
образца резины и перед погружением на
каждом образце делают какую-либо
идентификационную метку.
Погружают
образцы резины в соответствующее
устройство по 3.1 и 3.2, используя выбранную
жидкость (раздел 4) и заданную температуру
(6.1).
Для
полного погружения образцы размещают
на расстоянии не менее 5 мм от стенок
сосуда и не менее 10 мм от верхней и нижней
частей сосуда. Если плотность резины
меньше, чем плотность жидкости, должны
быть предусмотрены меры для того, чтобы
образцы для испытания полностью
находились ниже уровня жидкости.
Следует
устранить доступ воздуха. Если необходимо
испытать влияние воздуха, то степень
доступа воздуха может быть определена
по соглашению между заинтересованными
сторонами.
При
необходимости, в конце периода погружения
температуру образцов в течение 30 мин
приводят к стандартной лабораторной
температуре. Образцы для испытания
быстро перемещают в жидкость, имеющую
нужную температуру, и выдерживают в
течение 10-30 мин.
Удаляют
избыток жидкости для испытания с
поверхности образца. При использовании
летучих жидкостей образцы для испытания
вынимают и быстро промокают фильтровальной
бумагой или кусочком ткани, которые не
оставляют ворса. Вязкие нелетучие
жидкости можно удалить фильтровальной
бумагой и, при необходимости, быстро
обмакнуть образец для испытания в
летучую жидкость, такую как метанол или
петролейный эфир, а затем быстро
промокнуть.
При
извлечении образцов для испытания из
летучих жидкостей для испытания
необходимо, чтобы каждая последующая
процедура проходила по возможности
быстро. Все измерения проводят сразу
же после удаления избытка жидкости, а
для определения изменения массы или
объема образец резины немедленно
помещают в колбу для взвешивания.
Если
после измерения массы или размеров
используют те же образцы для определения
изменения других свойств, то их снова
погружают в летучую жидкость. Общее
время погружения должно соответствовать
требованиям 6.2. Максимальное время между
извлечением образца из жидкости для
испытания и окончанием измерения должно
быть не более:
-
изменение параметров - 1 мин;
-
изменение твердости - 1 мин;
-
испытание на растяжение - 2 мин.
Если
процесс погружения необходимо продолжить,
то сразу опускают образцы для испытания
в жидкость и возвращают их в сушильный
шкаф или водяную баню, где поддерживается
заданная температура.
Изменения
свойств образца можно также определить
после высушивания. Для этого высушивают
образец для испытания при давлении
воздуха 20 кПа и при температуре 40 °С до
постоянной массы, т.е. до тех пор, пока
разность между последовательными
взвешиваниями с интервалом 30 мин не
будет превышать 0,001 г. Охлаждают образец
до температуры (23±2) °С и кондиционируют
при этой же температуре не менее 3 ч.
7.2
Изменение массы
Взвешивают
каждый образец для испытания с точностью
до миллиграмма при стандартной
лабораторной температуре до и после
погружения.
Изменение
массы образца ,
%, вычисляют по формуле
,
(1)
где -
масса образца после погружения, мг;
-
масса образца до испытания, мг.
За
результат испытания принимают
среднеарифметическое значение показателя
трех испытанных образцов.
7.3
Изменение объема
Для
жидкостей, нерастворимых в воде,
используют метод вытеснения воды.
Взвешивают
каждый образец для испытания на воздухе
с точностью до миллиграмма ( ),
а затем еще раз взвешивают каждый образец
для испытания в дистиллированной воде
при температуре (23±2) °С ( );
необходимо, чтобы были удалены все
воздушные пузырьки (для этого можно
использовать моющее средство). Если
плотность материала образца равна 1
г/см ,
при взвешивании в воде необходимо
использовать груз, чтобы образцы для
испытания были полностью погружены.
При использовании груза отдельно
определяют его массу в дистиллированной
воде ( ).
Промакивают образцы для испытания
фильтровальной бумагой или кусочком
ткани, не оставляющими ворс.
Погружают
каждый образец для испытания в жидкость.
По окончании периода погружения
взвешивают каждый образец для испытания
на воздухе (масса )
с точностью до миллиграмма, а затем еще
раз взвешивают каждый образец для
испытания в дистиллированной воде
(масса )
при температуре (23±2) °С.
Изменение
объема образца ,
%, вычисляют по формуле
,
(2)
где -
масса образца для испытания после
погружения в жидкость, мг;
-
масса образца после погружения в воду
(плюс масса груза, при использовании),
мг;
-
масса груза в воде, при использовании,
мг;
-
начальная масса образца до испытания,
мг;
-
начальная масса образца до испытания
в воде (плюс масса груза, при использовании),
мг.
За
результат испытания принимают
среднеарифметическое значение показателя
трех испытанных образцов.
Если
жидкость для испытания легко смешивается
с водой или реагирует с ней, то воду не
следует использовать после погружения.
Если жидкость для испытания не слишком
вязкая или летучая при температуре
(23±2) °С, вместо воды можно использовать
новую порцию жидкости для испытания.
Если жидкость для испытания не подходит,
используют другую жидкость после
погружения и проводят расчеты следующим
образом
,
(3)
где -
плотность жидкости, г/см ;
-
масса образца до испытания в жидкости
(плюс масса груза, при использовании),
мг;
-
масса груза в жидкости, при использовании;
другие
обозначения - см. формулу (2).
7.4
Изменение размеров
Измеряют
начальную длину каждого образца для
испытания с точностью до 0,5 мм вдоль
осевой линии при стандартной лабораторной
температуре (проводят измерения по
нижней и верхней поверхностям и берут
среднее значение двух результатов).
Подобным образом измеряют начальную
ширину, сделав измерения в четырех
местах по верхней и нижней поверхностям
с каждого края образца для испытания.
Измеряют
начальную толщину образца для испытания
толщиномером в четырех различных местах
и рассчитывают среднеарифметическое
значение.
После
процедуры погружения образца в жидкость
снова измеряют длину, ширину и толщину
каждого образца для испытания, как
описано выше.
Все
измерения образца для испытания проводят
при стандартной лабораторной температуре.
Изменение
длины ,
%, вычисляют по формуле
,
(4)
где -
длина образца после погружения, мм;
-
начальная длина образца, мм.
Аналогично
рассчитывают процентные изменения
ширины и толщины образца.
Результаты
выражают как средние значения (медиана)
трех образцов для испытания.
Изменение
площади поверхности можно рассчитать,
исходя из полученных значений длины и
ширины.
7.5
Изменение площади поверхности
Измеряют
начальные длины диагоналей каждого
образца для испытания с точностью до
0,01 мм при стандартной лабораторной
температуре.
После
окончания процедуры погружения снова
измеряют длины диагоналей, как описано
выше; при использовании оптической
системы измерений это следует делать
в стеклянном сосуде, не извлекая образцы
из жидкости для испытания.
Изменение
площади поверхности вычисляют
по формуле
,
(5)
где и
-
длины диагоналей после погружения, мм;
и -
длины диагоналей до погружения, мм.
Изменение
объема ,
%, допускается вычислять по формуле
.
(6)
Формула
расчета изменения объема в процентах
предполагает изотропное набухание.
Если возникают сомнения, определяют
изменение объема в процентах, как указано
в 7.3, что является более предпочтительным
методом.
7.6
Изменение твердости
Измеряют
твердость твердомером IRHD каждого образца
для испытания до и после погружения,
используя микротест в соответствии с
ИСО 48.
В
качестве альтернативы можно использовать
твердость IRHD для трех сложенных образцов
для испытания, но в этом случае выражают
результат как кажущуюся твердость.
Рассчитывают
твердость образца IRHD до
и после погружения по формуле
,
(7)
где -
твердость после воздействия среды;
-
твердость до воздействия среды.
7.7
Изменение деформационно-прочностных
свойств при растяжении
Измеряют
физико-механические показатели при
растяжении до и после погружения в
соответствии с ИСО 37.
Рассчитывают
условную прочность при растяжении,
относительное удлинение при разрыве и
напряжение при заданном удлинении после
воздействия среды, используя начальное
поперечное сечение образца для испытания.
Рассчитывают изменение данного свойства
,
%, от значения для образца, который не
погружали в жидкость для испытания, по
формуле
,
(8)
где -
значение показателя после погружения,
мПа;
-
значение показателя до воздействия
среды, мПа.
7.8
Испытание при контакте жидкости только
с одной поверхностью
Данное
испытание применимо только к относительно
тонким листовым материалам, например
мембранам из резины, которые во время
использования подвергаются воздействию
жидкости только с одной поверхности.
Измеряют
первоначальную толщину образца для
испытания и затем взвешивают его на
воздухе с точностью до миллиграмма ( ).
Затем
помещают образец для испытания в
устройство, как показано на рисунке 1.
Наполняют камеру устройства жидкостью
для испытания до глубины 15 мм и закрывают
пробку 6. При проведении испытания в
устройстве поддерживают требуемую
температуру.
По
окончании периода контакта с жидкостью,
при необходимости, охлаждают устройство
до стандартной лабораторной температуры.
Удаляют жидкость и извлекают образец
для испытания. Избыток жидкости с
поверхности образца удаляют фильтровальной
бумагой или тканью, которые не оставляют
ворса. Затем взвешивают образец для
испытания с точностью до миллиграмма
( )
и измеряют толщину при стандартной
лабораторной температуре.
Если
жидкость для испытания при температуре
окружающей среды летучая, измерение
проводят в течение 2 мин после извлечения
образца из жидкости.
Вычисляют
изменение массы на единицу площади
поверхности по
формуле
,
(9)
где -
масса образца после испытания, г;
-
масса образца до испытания, г;
-
площадь поверхности образца для испытания
в форме кольца, находившегося в контакте
с жидкостью для испытания, м .
За
результат испытания принимают
среднеарифметическое значение измерений
трех образцов для испытания.
Изменение
толщины вычисляют, как описано в 7.4.
7.9
Определение количества экстрагируемых
веществ
7.9.1
Подготовка к испытанию
Если
жидкость для испытания легко летучая,
то массу веществ, которую она экстрагирует
из образца для испытания, можно определить
следующими способами:
a)
высушиванием обработанного образца
для испытания и сравнением его массы с
массой до погружения в жидкость или
b)
выпариванием жидкости для испытания
досуха и взвешиванием нелетучего
остатка.
Оба
способа предполагают ошибку. При
использовании способа а) резина может
окисляться, если при погружении
присутствовал воздух, особенно при
высоких температурах. При использовании
способа b) возможна некоторая потеря
летучих экстрагируемых веществ, особенно
пластификаторов. Выбор способа определения
массы зависит от свойств испытуемого
материала и условий испытания.
Для
испытаний не рекомендуется применять
жидкости с температурой кипения выше
110 °С.
Определение
количества экстрагируемых веществ
следует проводить после определения
изменения массы (7.2), изменения объема
(7.3) и изменения размеров (7.4).
7.9.2
Взвешивание высушенного образца для
испытания
Высушивают
образец для испытания после погружения
при абсолютном давлении воздуха 20 кПа
и температуре (40±2) °С до постоянной
массы, т.е. до тех пор пока разность между
последовательными взвешиваниями с
интервалом 30 мин не будет превышать
0,001 г.
Массу
экстрагируемых веществ берут как
разность между первоначальной массой
образца для испытания и его массой после
погружения и высушивания и выражают в
процентах от первоначальной массы
образца для испытания.
7.9.3
Выпаривание жидкости для испытания
Переливают
жидкость для испытания, в которую был
погружен образец резины, в сосуд,
промывают образец для испытания 25 мл
новой жидкости и собирают промывные
воды в тот же сосуд, выпаривают эту
жидкость и высушивают остаток до
постоянной массы при абсолютном давлении
воздуха 20 кПа и температуре(40±2) °С.
Проводят
контрольное испытание для оценки
содержания твердых веществ в объеме
жидкости для испытания, равном объему
жидкости, используемому для погружения
образца и его промывания.
Содержание
экстрагируемых веществ вычисляют как
массу сухого остатка с поправкой на
результат контрольного испытания,
выраженную в процентах от начальной
массы образца для испытания.
8
Протокол испытания
Протокол
испытания должен содержать:
a)
ссылку на настоящий стандарт;
b)
подробные данные об образце:
1)
полное описание образца и его происхождение;
2)
состав резиновой смеси, условия
вулканизации, при необходимости, интервал
времени между вулканизацией и испытанием;
3)
метод приготовления образцов для
испытания, например путем формования
или вырубания;
4)
полное описание жидкости для испытания.
В случае минеральных масел (кроме
стандартных масел 1, 2 и 3) необходимо
указывать плотность, вязкость, коэффициент
преломления и анилиновую точку или
содержание ароматических соединений;
c)
метод испытания и подробное описание:
1)
используемый(е) метод(ы);
2)
тип образца для испытания (размеры);
3)
используемую температуру испытания;
4)
кондиционирование;
5)
продолжительность и температуру
погружения;
6)
любое отклонение от заданной методики;
d)
результаты испытания:
1)
результаты, выраженные в форме,
установленной в соответствующем разделе;
2)
описание внешнего вида образца резины
для испытания (например, растрескивание,
расслаивание), при необходимости;
3)
описание внешнего вида жидкости для
испытания (например, обесцвечивание,
осаждение), при необходимости;
e)
дату проведения испытания.
Приложение
А
(обязательное)
Стандартные жидкости
Предупреждение
- Следует соблюдать соответствующие
меры предосторожности при подготовке
и обращении с жидкостями для испытания,
особенно с токсичными, коррозионно-агрессивными
или воспламеняющимися.
С
продуктами, выделяющими сажу, необходимо
работать только в вытяжном шкафу с
хорошей вентиляцией, коррозионно-агрессивные
продукты не должны попадать на кожу или
обычную одежду, а воспламеняющиеся
продукты необходимо хранить вдали от
источника воспламенения.
А.1
Стандартные моделируемые топлива
Промышленное
топливо даже в пределах одной марки
(т.е. одной детонационной стойкости) и
из одного источника сильно различается
по составу. Топливо может быть на основе
углеводородов, содержащих и не содержащих
кислородные соединения, а также на
основе спирта. Октановое число бензина
повышается при наличии ароматических
или кислородных соединений, однако эти
добавки увеличивают воздействие топлива
на обычно стойкие к воздействию топлив
резины. Состав топлива различают в
зависимости от состояния рынка бензина
и географического местоположения,
причем изменения могут происходить
быстро.
Поэтому
в таблицах А.1 и А.2 рекомендованы несколько
жидкостей для испытания. Для приготовления
жидкостей для испытания следует
использовать материалы, чистота которых
соответствует чистоте аналитических
реактивов. Не используют жидкости для
испытания, содержащие спирт, если
известно, что топлива для испытания не
содержат спирт.
Таблица
А.1 - Стандартные моделируемые топлива,
не содержащие кислородные соединения
|
|
|
Жидкость
для испытания
|
Компонент
|
Содержание,
% об.
|
А
|
-
2,2,4-Триметилпентан
-
|
100
|
В
|
-
2,2,4-Триметилпентан
-
|
70
|
-
|
-
Толуол
-
|
30
|
С
|
-
2,2,4-Триметилпентан
-
|
50
|
-
|
-
Толуол
-
|
50
|
D
|
-
2,2,4-Триметилпентан
-
|
60
|
-
|
-
Толуол
-
|
40
|
Е
|
-
Толуол
-
|
100
|
F
|
-
Парафины
с прямой цепью (С
до C )
-
|
80
|
-
|
-
1-Метилнафталин
-
|
20
|
Примечание -
Жидкости В, С и D являются моделями
легкого топлива, не содержащего
кислородных соединений. Жидкость F
предназначена для моделирования
дизельного топлива, топлива
коммунально-бытового назначения и
аналогичного легкого печного топлива.
|
Таблица
А.2 - Стандартные моделируемые топлива,
содержащие кислородные соединения
(спирты)
|
|
|
Жидкость
для испытания
|
Компонент
|
Содержание,
% об.
|
1
|
-
2,2,4-Триметилпентан
-
|
30
|
-
|
-
Толуол
-
|
50
|
-
|
-
Диизобутилен
-
|
15
|
-
|
-
Этанол
-
|
5
|
2
|
-
2,2,4-Триметилпентан
-
|
25,35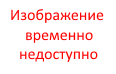
|
-
|
-
Толуол
-
|
42,25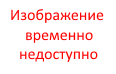
|
-
|
-
Диизобутилен
-
|
12,68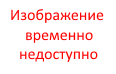
|
-
|
-
Этанол
-
|
4,22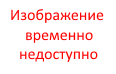
|
-
|
-
Метанол
-
|
15,00
|
-
|
-
Вода
-
|
0,50
|
3
|
-
2,2,4-Триметилпентан
-
|
45
|
-
|
-
Толуол
-
|
45
|
-
|
-
Этанол
-
|
7
|
-
|
-
Метанол
-
|
3
|
4
|
-
2,2,4-Триметилпентан
-
|
42,5
|
-
|
-
Толуол
-
|
42,5
|
-
|
-
Метанол
-
|
15
|
-
Вместе эти
четыре компонента составляют 84,5% об.
жидкости для испытания 1.
-
|
А.2
Стандартные масла
А.2.1
Общие сведения
А.2.1.1
Масло N 1 (Масло ASTM N 1)
Масло
с малым увеличением объема, состоящее
из тщательно контролируемой смеси
минеральных масел, включающей
экстрагированный растворителем,
химически обработанный и депарафинированный
остаток, и нейтральное масло.
А.2.1.2
Масло N 2 (IRM 902)
Масло
со средним увеличением объема, полученное
экстракцией растворителем и обработкой
кислотой и глиной дистиллята высокой
вязкости из сырой нефти, добытой на
побережье Персидского залива, с высоким
содержанием нафтеновых углеводородов.
А.2.1.3
Масло N 3 (IRM 903)
Масло
с высоким увеличением объема, состоящее
из тщательно контролируемой смеси двух
фракций смазочных масел, полученных
путем вакуумной перегонки из сырой
нефти, добытой на побережье Персидского
залива, с высоким содержанием нафтеновых
углеводородов.
А.2.1.4
Предполагаемое использование
Данные
стандартные масла представляют собой
минеральные масла с низким содержанием
присадок. Стандартные масла для
моделирования масел с высоким содержанием
присадок или синтетических масел
находятся в стадии разработки.
А.2.2
Требования
Данные
масла не должны содержать присадок, за
исключением, возможно, следов (примерно
0,1%) депрессорной присадки, а также должны
иметь свойства в соответствии с таблицей
А.3. Свойства по таблице А.4 являются
типичными для этих масел, но изготовитель
их не гарантирует.
Таблица
А.3 - Требования к стандартным маслам
|
|
|
|
|
Наименование
показателя
|
Значение
для масла
|
Метод
испытания
|
|
N 1
|
N 2
|
N 3
|
|
Анилиновая
точка, °С
|
124±1
|
93±3
|
70±1
|
ИСО
2977
|
Кинематическая
вязкость, м /с
( 10 )
|
20±1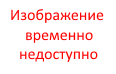
|
20±1
|
33±1
|
ИСО
3104
|
Температура
вспышки, °С, не ниже
|
243
|
240
|
163
|
ИСО
2592
|
Плотность
при температуре 15 °С, г/м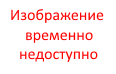
|
0,886±0,002
|
0,933±0,00
|
0,921±0,00
|
ИСО
3675
|
Вязкостно-гравитационная
константа
|
-
|
0,865±0,005
|
0,880±0,005
|
-
|
Содержание
нафтенов ,
%
|
-
|
35
|
40
|
-
|
Содержание
парафинов ,
%
|
-
|
50
|
45
|
-
|
-
Измерения
проводились при температуре 99 °С.
-
-
Измерения
проводились при температуре 37,8 °С.
-
|
Таблица
А.4 - Типичные свойства стандартных масел
|
|
|
|
|
Наименование
показателя
|
Значение
для масла
|
Метод
испытания
|
|
N 1
|
N 2
|
N 3
|
|
Температура
потери текучести, °С
|
-
|
-12
|
-31
|
ИСО
3016
|
Показатель
преломления при температуре 20 °С, мин
|
1,4860
|
1,5105
|
1,5026
|
ИСО
5661
|
Содержание
ароматических соединений ,
%
|
-
|
12
|
14
|
-
|
Примечание
- Стандартные масла N 1, N 2 и N 3 идентичны
стандартным маслам по стандарту АСТМ
Д 471-95 "Стандартный метод определения
свойств резины. Воздействие жидкостей"
как масло ASTM N 1, IRM 902 и IRM 903 соответственно.
Стандартные масла IRM 902 и IRM 903 заменены
на стандартные масла N 2 и N 3 соответственно
согласно предыдущему изданию стандарта
АСТМ Д 471-91. Ранее применяемые масла были
идентичны стандартным маслам N 2 и N 3 в
ИСО 1817:1985. Масло N 1 не изменилось.
Если
в качестве жидкостей для испытаний
применяют эти стандартные масла, следует
использовать масла только от признанных
поставщиков как для поверочных целей,
так и для общих целей. В случае отсутствия
таких масел можно использовать
альтернативные масла, но только для
проведения типовых испытаний, при
условии соответствия масел требованиям,
указанным в таблице А.3, а также, если
известно, что их использование дает
такие же результаты, как и при использовании
стандартных масел при испытании резин,
по составу аналогичных резинам, которые
используют в типовых испытаниях.
В
таблицах А.3 и А.4 представлены технические
требования и свойства стандартных
масел, однако основным параметром
является влияние этих масел на физические
свойства резин после погружения в
жидкость. Ряд испытаний показал, что
воздействие новых масел N 2 и N 3 может
быть менее агрессивным, чем ранее
применяемых масел. Поэтому если испытания
проводят со старыми маслами N 2 и N 3, то
рекомендуется пользоваться программами
испытаний, по которым проводится прямое
сравнение воздействия старых и новых
стандартных масел на отдельные соединения
и изделия.
А.3
Моделируемые рабочие жидкости
А.3.1
Жидкость 101
Жидкость
101 предназначена для моделирования
синтетических смазочных масел из сложных
диэфиров. Она представляет собой смесь,
состоящую из 99,5% масс. ди-2-этилгексилсебацината
и 0,5% масс. фенотиазина.
А.3.2
Жидкость 102
Жидкость
102 предназначена для моделирования
определенных смазочных масел с высоким
гидравлическим давлением.
Это
смесь, состоящая из 95% масс. масла N 1 и
5% масс. углеводородной присадки,
содержащей 29,5% масс. - 33% масс. % серы, 1,5%
масс. - 2% масс. фосфора и 0,7% масс. азота.
А.3.3
Жидкость 103
Жидкость
103 предназначена для моделирования
масел из сложного эфира фосфорной
кислоты для гидравлических систем,
используемых в авиации. Это три-н
-бутилфосфат.
А.4
Химические реактивы
Испытания
химическими реактивами следует проводить
с теми же химическими продуктами и в
тех же концентрациях, какие применяют
при эксплуатации изделий из резины.
Приложение
ДА
(справочное)
Сведения о соответствии
ссылочных международных стандартов
ссылочным национальным стандартам
Российской Федерации (и действующим в
этом качестве межгосударственным
стандартам)
Таблица
ДА.1
|
|
|
Обозначение
ссылочного международного стандарта
|
Степень
соответствия
|
Обозначение
и наименование соответствующего
национального стандарта
|
-
ИСО 37
|
NEQ
|
ГОСТ
270-66** "Резина. Метод определения
упруго-прочностных свойств при
растяжении"
|
_______________
* Вероятно,
ошибка оригинала. Следует читать:
ГОСТ 270-64. На территории Российской
Федерации документ не действует.
Действует ГОСТ 270-75. - Примечание
изготовителя базы данных.
-
|
-
ИСО 48
|
NEQ
|
ГОСТ
20403-75 "Резина. Метод определения
твердости в международных единицах
(от 30 до 100 IRHD)"
|
-
ИСО 175
|
-
|
*
|
-
ИСО 2592
|
-
|
*
|
-
ИСО 2977
|
NEQ
|
ГОСТ
12329-77 "Нефтепродукты и углеводородные
растворители. Метод определения
анилиновой точки и ароматических
углеводородов"
|
-
ИСО 3016
|
MOD
|
ГОСТ
20287-91 "Нефтепродукты. Метод определения
температуры текучести и застывания"
|
-
ИСО 3104
|
MOD
|
ГОСТ
33-2000 (ИСО 3104-94) "Нефтепродукты.
Прозрачные и непрозрачные жидкости.
Определение кинематической вязкости
и расчет динамической вязкости"
|
-
ИСО 3675
|
IDT
|
ГОСТ
Р ИСО 3675-2007 "Нефть сырая и нефтепродукты
жидкие. Лабораторный метод определения
плотности с использованием ареометра"
|
-
ИСО 5661
|
-
|
*
|
-
ИСО
23529:2004
|
NEQ
|
ГОСТ
269-66 "Резина. Общие требования к
проведению физико-механических
испытаний"
|
* Соответствующий
национальный стандарт отсутствует.
До его утверждения рекомендуется
использовать перевод на русский язык
данного международного стандарта.
Перевод данного международного
стандарта находится в Федеральном
информационном фонде технических
регламентов и стандартов.
Примечание -
В настоящей таблице использованы
следующие условные обозначения
степени соответствия стандартов:
- IDT
- идентичные стандарты;
- MOD
- модифицированные стандарты;
- NEQ
- неэквивалентный стандарт.
|
Электронный
текст документа
подготовлен ЗАО
"Кодекс" и сверен по:
официальное
издание
М.: Стандартинформ,
2011
|